Products Description
Alloy 400, also known as UNS N04400 or Monel 400, is a ductile nickel-copper alloy that offers excellent resistance to various corrosive conditions. It is commonly used in environments that range from mildly oxidizing to neutral, as well as moderately reducing conditions.One of the notable features of Alloy 400 is its resistance to corrosion by a wide range of substances, including seawater, steam, salt, and caustic solutions. This makes it particularly well-suited for applications in marine environments and other nonoxidizing chloride solutions.The alloy exhibits good mechanical properties over a wide temperature range and is often used in applications such as chemical processing, marine engineering, hydrocarbon and petrochemical processing, and equipment for the production of gasoline, freshwater, and steam.It's worth noting that Alloy 400 has a relatively low corrosion rate in flowing seawater but can be susceptible to stress corrosion cracking in certain conditions. Therefore, it is essential to consider the specific operating conditions and consult the alloy's manufacturer or a materials engineer for guidance on its suitability for a particular application.
Applications
- Chemical Processing Equipment – in fluorine, hydrofluoric acid, hydrogen fluoride, hydrochloric acid, sulfuric acid, neutral and alkaline salt solutions, caustic alkalies, non-oxidizing halides and dry chlorine service.
- Marine Components – shipbuilding, valves, pumps, shafts and in sea and brackish water
- Oil and Gas Production – splash-zones for offshore structures and sour gas applications
- Ore Processing – uranium refining and separation in the production of nuclear fuels
- Petroleum Refining – alkylation units, crude petroleum stills, piping and storage tanks
- Power Generation – feed-water heaters and steam generators
- Water Treatment – brine heaters and evaporators in seawater desalination plants
Standards
ASTM..................B 127ASME..................SB 127
AMS ...................4544
Federal............... QQ-N-281
General Properties
Alloy 400 (UNS N04400) is a nickel-copper alloy that offers excellent resistance to a wide range of corrosive environments. It is known for its resistance to chloride stress corrosion cracking, making it highly suitable for applications in marine and chemical processing industries where exposure to chlorides is common.One of the advantages of Alloy 400 is its high strength and toughness, which are maintained over a broad temperature range. This property makes it suitable for various operating conditions.Alloy 400 is extensively used in corrosive applications where it can be exposed to chemicals, saltwater, and other aggressive environments. It finds applications in marine equipment, chemical processing equipment, valves, pumps, heat exchangers, and various other components.The alloy can be readily fabricated using conventional processing operations such as hot and cold working, machining, and welding. This makes it convenient for manufacturers to work with and produce complex components.Additionally, there is a variant of Alloy 400 called Alloy 400AR, which is produced in the as-rolled condition to meet higher strength requirements. This variant offers enhanced strength while retaining many of the corrosion-resistant properties of the base alloy.It's important to note that while Alloy 400 has excellent corrosion resistance, it may not be suitable for highly oxidizing environments or environments containing strong acids. In such cases, it is advisable to consult with materials engineers or alloy manufacturers to determine the best choice for the specific application.
Chemical Analysis
Weight % (all values are maximum unless a range is otherwise indicated)
|
|
|
|
Nickel (plus Cobalt) |
63.0 min.-70.0 max. |
Iron |
2.50 |
Copper |
28.0 min.-34.0 max. |
Sulfur |
0.024 |
Carbon |
0.3 |
Silicon |
0.5 |
Manganese |
2.0 |
|
|
Physical Properties
Density
0.318 lbs/in38.80 g/cm3
Specific Heat
0.102 BTU/lb-°F (68°F)427 J/kg-°K (20°C)
Modulus of Elasticity
26.4 x 103 ksi (68°F)182 GPa (20°C)
Thermal Conductivity 200°F (100°C)
150 BTU/hr/ft2/ft/°F (68°F)22.0 W/m-°K (20°C)
Melting Range
2370 – 2460°F1300 – 1350°C
Electrical Resistivity
307 Microhm-in at 70°C0.511 Microhm-cm at 21°C
Temperature |
Mean Linear Expansiona |
||
°F |
°C |
in/in/°F x 10-6 |
um/m•°C |
-320 |
-200 |
— |
— |
-300 |
-180 |
6.1 |
11.1 |
-200 |
-130 |
6.4 |
11.4 |
-100 |
-70 |
6.7 |
12.1 |
70 |
21 |
— |
— |
200 |
100 |
7.7 |
14.2 |
400 |
200 |
8.6 |
15.2 |
600 |
300 |
8.8 |
15.7 |
800 |
400 |
8.9 |
16.1 |
1000 |
500 |
9.1 |
16.3 |
1200 |
600 |
9.3 |
16.6 |
1400 |
700 |
9.6 |
17.0 |
1600 |
800 |
9.8 |
17.4 |
1800 |
900 |
10.0b |
17.7 |
2000 |
1000 |
10.3b |
18.1b |
(a) annealed material, (b) extrapolated
Mechanical Properties
Nominal Room-Temperature Mechanical Properties of Alloy 400 and 400AR
FORM AND CONDITION |
Yield Strength |
Tensile Strength |
Elongation, % |
Hardness |
|||
ksi |
MPa |
ksi |
MPa |
Brinell |
Rockwell |
||
Plate |
|
|
|
|
|
|
|
Hot-Rolled, As-Rolled |
40-75 |
276-517 |
75-95 |
517-655 |
45-30 |
125-215 |
70-96 |
Hot-Rolled, Annealed |
28-50 |
193-345 |
70-85 |
482-586 |
50-35 |
110-140 |
60-76 |
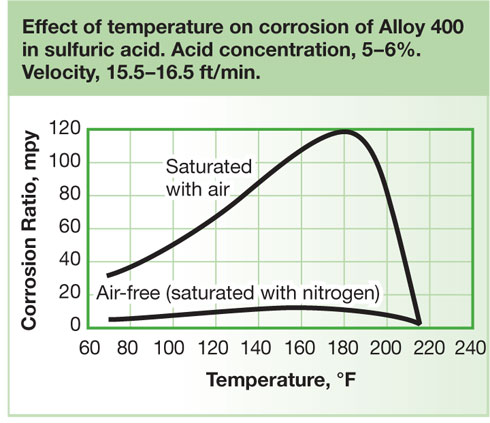
MATERIAL |
Corrosion Rate, mpy (mm/a) |
Alloy 400 |
22 (0.56) |
Nickel 200 |
>200 (>5.08)b |
Alloy 600 |
150 (3.81) |
AISI 304 Stainless Steel |
>210 (>5.33)b |
AISI 316 Stainless Steel |
>190 (>4.83)b |
Mild Steel |
>170 (4.32) |
(a) Acid contains 1.5-2.5% fluosilicic acid, 0.3-1.25% sulfuric acid, and 0.01-0.03% iron. Test specimens immersed in solution in storage tank. Temperature, 60-80°F (15-27°C); duration of test, 28 days.
(b) Specimen completely destroyed during test.
Resistance of Nickel Alloys to Impingement Attack by Seawater at 150 ft/sec (45.7 m/s)
ALLOY |
Corrosion/Erosion Rate |
|
|
mpy |
mm/a |
Alloy 625 |
Nil |
Nil |
Alloy 825 |
0.3 |
0.008 |
Alloy K-500 |
0.4 |
0.01 |
Alloy 400 |
0.4 |
0.001 |
Alloy 200 |
40 |
1.0 |
Fabrication Data
Alloy 400 is readily fabricated by conventional processing operations.
Hot Working
Alloy 400 is a relatively soft material that is receptive to hot forming into almost any shape. The range of hot forming temperatures is 1200 - 2150°F (649 - 1177°C). For heavy reductions the recommended temperature range is 1700 – 2150°F (927 – 1177°C). Light reductions are possible with temperatures as low as 1200°F (649°C). Working at lower temperatures will result in higher mechanical properties and smaller grain size.
Cold Working
Alloy 400 is readily cold worked by virtually all cold fabrication methods. Cold working should be performed on annealed material. The alloy has a somewhat higher work hardening rate than carbon steel, but not as high as 304 stainless steel.
Machining
Alloy 400 can be machined at standard rates with conventional machine tools. Surface cutting speeds should be low compared to those used for carbon steel due to the alloy’s high work-hardening rate.
Welding
Alloy 400 can be welded to itself or dissimilar metals by utilizing conventional welding processes. These include conventional or hot wire GTAW (TIG), plasma arc, GMAW (MIG/MAG) and SMAW (MMA). The choice of welding product is dependent upon the materials being welded and the environment in which it occurs.