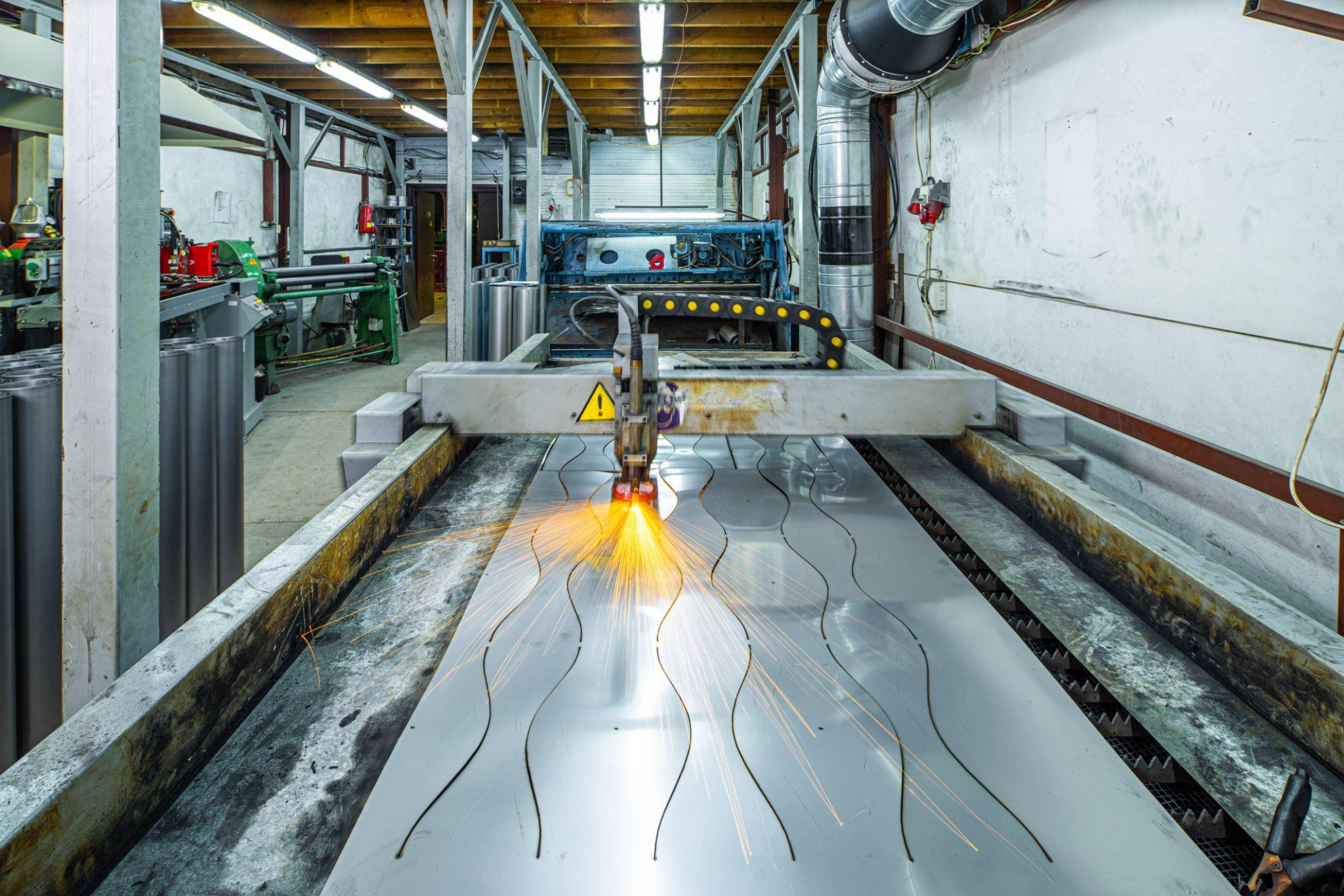
Stainless steel cutting type
1Principle of plasma cutting machine:
Principle of Plasma Cutting Machine
Compressed air is used as the working gas, and the high-temperature and high-speed plasma arc is used as the heat source to partially melt the cut metal, and at the same time, the high-speed airflow blows away the melted metal to form a narrow slit. This equipment can be used for cutting various metal materials such as stainless steel, aluminum, copper, cast iron, carbon steel, etc. It not only has fast cutting speed, narrow slit, flat cut, small heat-affected zone, low workpiece deformation, simple operation, and significant energy saving effect. This equipment is suitable for the manufacture, installation and maintenance of various machinery, metal structures, and cutting, drilling, digging, and beveling of middle and thin plates.
Operating procedures of plasma cutting machine:
1.1 In order to reduce energy consumption and increase the life of nozzles and electrodes, when cutting thinner workpieces, "low-grade" cutting should be used as much as possible.
1.2 When the "cut thickness selection" switch is set to "high-end", non-contact cutting should be used (except in special circumstances) and the water cutting torch should be preferred.
1.3 When it is necessary to change the "thickness selection" switch position, be sure to turn off the power switch of the host first to prevent damage to the machine parts.
1.4 When assembling, disassembling or moving the host, be sure to turn off the power supply before proceeding to prevent danger.
1.5 Turn off the power switch of the host before installing and disassembling the accessories and parts (such as cutting torch, cutting ground wire, electrode, nozzle, distributor, pressure cap, protective cover, etc.) on the host. Avoid turning on the torch switch repeatedly and quickly to avoid damage to the arc ignition system or related components.
1.6 When it is necessary to start arc cutting from the middle of the workpiece, cut stainless steel ≤ 20mm thick, and can directly perforate and cut. The method is: place the cutting torch at the starting point of the slit, and make the cutting torch nozzle axis and the workpiece plane at an angle of about 75°, then turn on the torch switch to start the arc perforation; at the same time, slowly adjust the nozzle axis and the workpiece The angle between the faces should be adjusted to 90° when cutting through the workpiece. After cutting through the workpiece, cut normally along the slitting direction. However, if perforation and cutting are required when the thickness exceeds the above-mentioned thickness, a small hole must be drilled at the cutting starting point (the diameter is not limited), and the arc is cut from the small hole. Otherwise, it is easy to damage the torch nozzle.
2Laser cutting:
Principle of metal laser cutting machine
The metal laser cutting machine uses a metal laser with a xenon lamp as the excitation source to output a high-energy-density laser beam and focus on the surface of the workpiece, so that the area irradiated by the spot on the workpiece is melted and vaporized instantaneously, and moved by a computer-controlled numerical control mechanical system. The spot illuminates the position to realize automatic cutting. It is a high-tech equipment integrating laser technology, numerical control technology and precision machinery technology.
Features of metal laser cutting machine
★Good cutting quality, small deformation, smooth and beautiful appearance.
★Fast cutting speed, high efficiency, low cost, safe operation and stable performance.
★Imported servo motor and oriented transmission mechanism are adopted, and the cutting precision is high.
★Using professional software, various graphics or texts can be designed at will for instant processing, flexible processing, simple and convenient operation.
★The laser beam is easy to realize time or space splitting, and it can process multiple beams at the same time or multi-station sequential processing.
Application field
★Laser cutting machine, commonly known as laser cutting machine, can cut metal, a variety of non-metallic sheets and pipes. It is especially suitable for cutting stainless steel, iron, aluminum, ceramic, silicon, diamond and other materials.
★Widely used in sheet metal, hardware, steel structure, precision machinery, auto parts, glasses, jewelry, nameplates, advertising, handicrafts, electronics, toys, packaging and other industries.
3 Water cutting:
Water jets are widely used in high-volume applications worldwide. It is complementary to other technologies (milling machine, laser, EDM, plasma and planer). Waterjet cutting does not use toxic gases or liquids, and does not produce toxic substances or vapors. The waterjet cutting surface does not leave any HAZ or mechanical deformation. It is a truly versatile, high-efficiency cold cutting technology. Waterjet has proven that it can complete tasks that other technologies cannot handle. From cutting extremely thin details on stone, glass and metal, quickly drilling holes in titanium alloys, cutting food, and sterilizing beverages and solutions, the water jet has proven its unique value. Essentially, there are two types of water jets: (1) pure water jets and (2) sanded water jets. The equipment is designed to use only pure water jets, only sanding water jets, or both. Regardless of the form, the water must first be pressurized. Two types of waterjets: Two types of waterjets refer to pure water jets and sanded water jets. Both have proven and unique properties.
Pure water jet
The pure water jet is the earliest water cutting method. The first commercial application began in the mid-1970s for cutting corrugated cardboard. The biggest applications of pure water jets are cutting disposable diapers, tissue paper and automotive interior parts. For tissue paper and disposable diapers, compared with other technologies, water jet technology leaves the least moisture on the material. In some diaper or tissue factories, unplanned downtime is very common for other cutting technologies and can cost more than $20,000 per hour. The waterjet provides continuous operation throughout the year for this application-maintenance operations can be incorporated into the production process.
Features of pure water jet
·Very fine water flow (common diameter range: 0.004 to 0.010 inches)
·Very detailed geometric shapes
·Very little material cutting loss
·No heat is generated when cutting
·The cutting thickness can be very large
·Can also be cut very thin
·Fast cutting speed
·Able to cut soft and lightweight materials (such as fiber glass insulation materials up to 24" thick)
·Minimal cutting force
·Simple fixture
Continuous operation 24 hours a day
How high is the temperature of the Mach 3 water jet?
When the water is accelerated to a high speed, the temperature of the water will rise. As the water flows out of the nozzle, friction and other factors heat the water flow. Take the inlet water temperature as the starting point. For every 1000 psi increase, the water temperature rises by 2 to 3 degrees. Therefore, the temperature of the water in Mach 3 is about 170 to 180 degrees Fahrenheit.
Pure water waterjet cutting head
As mentioned earlier, the basic waterjet process includes water flowing out of the pump, passing through the pipe, and outputting from the cutting head.
In waterjet cutting, the material removal process can be called supersonic erosion technology. It is not the pressure that removes the material particles, but the speed of the water flow. Pressure and speed are two completely different forms of energy. But how is the water pressure of the pump converted into another form of energy (ie water velocity)? The answer is a small gem. There is a gem at the end of the tube. There is a tiny hole in the gem. High-pressure water flows out through this small opening, thereby converting pressure into speed. At about 40,000 psi, the water flowing out of the nozzle moves at a speed of Mach 2. At 60000 psi, the speed exceeds Mach 3.
For ordinary cutting, the diameter of the pure water jet nozzle ranges from 0.004 to 0.010 inches. When using a tractor to move the nozzle back and forth to wash the concrete, a single large nozzle is commonly used, with a maximum diameter of 1/10 inch.
The three commonly used nozzle materials (sapphire, ruby, diamond) each have their own unique properties. Sapphire is now the most commonly used nozzle material. It is a man-made single crystal gem. Its water flow quality is quite good; it has a cutting life of about 50 to 100 hours under good water quality conditions. In the application of sanding waterjet, the life of sapphire is 1/2 of that of pure waterjet application. Under normal circumstances, the price of sapphire is between 15 to 30 US dollars per block.
Ruby can also be used for abrasive waterjet applications. Its water flow characteristics are very suitable for sanding waterjets, but not very suitable for pure water waterjet cutting. Its cost is about the same as that of sapphire.
Diamonds have a much longer lifespan (800 to 2000 hours), but the price is 10 to 20 times higher. Diamonds are very useful in situations that require continuous operation 24 hours a day. Unlike other types of nozzles, diamonds can sometimes be ultrasonically cleaned and reused.
Sanding waterjet
There are only a few differences between sand waterjet and pure water waterjet. In pure water jets, materials are eroded by supersonic water. In the sanding waterjet, sand particles are accelerated by a water jet, and these particles (not water) erode the material. The ability of sanding water jet is hundreds of times stronger than pure water jet. Both pure water jets and sand jets are useful. Pure water jets can cut soft materials, while sanded water jets cut hard materials such as steel, stone, composite materials and ceramics. The sanding waterjet with standard parameters can cut materials with a hardness equal to (or even slightly higher than) alumina ceramics (often called alumina, AD 99.9). We will introduce the characteristics of the abrasive waterjet and the working method of the abrasive waterjet cutting head below.
Features of sanding water jet
·Extremely versatile technology
·No HAZ
·No mechanical stress
·Easy to program
· Thin water flow (0.020 to 0.050 inches in diameter)
Can cut very complex geometric shapes
·Thin material cutting
· 10 inch thickness cutting
·Stacked cutting
·Material cutting loss is very small
·Simple fixture
·Small cutting force (less than 1 pound when cutting)
·It only needs to be set once for almost all sanding waterjet operations
·Easy to switch from single cutting head to multiple cutting heads
Can quickly switch from pure water jet to sand jet
·Reduce auxiliary operations
· Few or no burrs
Sand waterjet cutting head
Each sanding water jet includes a pure water jet. After the pure water jet is formed, sand is added. The sand particles are then accelerated along the knife tube, just like a rifle bullet. The sand used for sanding waterjet cutting is hard sand of uniform size after special screening. The most commonly used sand is garnet. Garnet is hard, strong and cheap. Like the pink sandpaper in a hardware store, different sizes are used for different jobs:
120 Mesh-produces a smooth surface
80 Mesh-the most commonly used, general purpose
50 Mesh-The cutting speed is a bit faster than 80 Mesh, but the surface is slightly rougher
The knife barrel accelerates sand particles like a rifle barrel. Similar to the nozzle, the knife tube has many different sizes and lifespans. The knife tube is approximately 3 inches long and 1/4 inch in diameter; the inner diameter ranges from 0.020 to 0.060 inches, and the most commonly used is 0.040 inches.
Although sanding waterjet equipment is often regarded as simple and reliable equipment, the knife tube needs to be paid attention to by the operator. The main advancement of waterjet technology is the invention of a long-life knife tube. Unfortunately, the long-life knife tube is much weaker than the previous tungsten carbide tube. If the cutting head hits the fixture, heavy object, or target material, the knife tube may break. The broken pipe cannot be repaired. At present, the most advanced system is equipped with an anti-collision detection device to protect the knife tube.